so
[Pw
s]
to the controller will show the output names.
PUMP OFF R1
renamed by [Pw ER1 POMP]
Lamp ON 320 R2 by [0000 ER2 Lamp]
R4
OFF no
R3! renamed by [Pw ER3 3]
etc.... Default name is always used
to rename an output
After editing, the Alias will be used to
command any switching on the outputs. So
choose short, meaningful and easy-to-remember output names. To
switch On the PUMP for 15
minutes and the Lamp for 1H,
send command [Pw pump 900 Lamp 3600]
where lower/upper cases are of no importance.
To name or to
rename the controller.
Command Dai found at menu D
for Data and GPRS gives the
possibility to give a name to the controller. This will be very
convenient when more than a single controller need to be monitored. The
name will then appear at the end of the received message from the
controllers,.
To name it Paris-02
use [0000
Dai Paris-02] to remove the name [0000
Dai ] (2 spaces after Dai)...
EZn to change the two characters
of Z1 Z2 Z3
This only can change to the two letters showing
Z1, Z2 and
Z3, but does not raise any
influence on the functionality. These functions can be used for
different sensors and therefore could better be listed by meaningful
alias.
So a pressure sensor on Z1 could be aliased by P1, another on Z2 could
be shown by GL and a Voltmeter on Z3 could be named V8.
For example: [
0000
ez3 V8 ez1 P1 ez2 GL]
could do it all together...
EPM EP1 EP2 EP3
To name the PMC, phases or groups
The optional
Power
Meter
Controller , its three phases or
three groups of mono phases can also all be named. These names are only
shown when accessing the controller via internet, but do not interfere
with any functionality (see
PM).
EFnn To
name the functions V1 to Z3
Functions V1, V2, V3, Vs, L0, L1, L2, L3, T1, T2, Z1, Z2, Z3 can also
be named with up to 15 characters names. These names will be visible on
the web page and on Alert- and Warning-SMS messages giving more meaning
the the above abbreviations.
The controller's built-in server sends all the system infos on a single
web page where different fields will show these edited names. The
interface is obvious and a careful look will reveal almost all the
function names and passing the PC mouse through a field adds more info
at the tool tips.
To check the difference between internet and SMS mode, only write
0000
s at the
navigator screen
command line and push on the gray [Send]
button. The normal status SMS will then also be visible at page refresh
at the bottom. This works also for the other commands that will show
the reply SMS at page bottom.Commands send via SMS, internet or PC will
all have same syntax and do not need [ ] delimiters brackets included.
To name T1 in "
Thermometer
1" send command [
0000
EFT1 Thermometer_1]. For
L1
[
0000
EFL1 Phase_1]. Note here that because of the limited
compatibility between languages, systems and navigators,
punctuation marks should best be
avoided.
For V1 send command [
0000
EFV1 Battery_G1], V2 [
0000
EFV2 Group_48V], V3, [
0000
EFV3 Batt_G2] ,,,
For Z1 to Z3 [
0000
EFz2 Oil_tank_G2]. Do not confuse Zn alias (at EZn above) with
Zn function names.
The
Fw1 to
Fw4 have a particular functionality
as explained in the "Functions expert" file...
Pw
Password (default 0000). [Pw
P?] for infos.
The password shown
as Pw
in the example is 0000 (4xZERO) by default
.
To change it, send SMS [OldPassword
P(NewPassword)].
The password is 3 to 7 characters maxi, alphanumeric
digits and/or letters and is case
sensitive with no blank in it! Keep it short to make things fast
and easy. So [0000
P(911)].
To change it to
ABC, send
SMS [
0000
P(ABC)] and to change it again for "1+2=3" send [
ABC
P(1+2=3)]
If the password is lost or forgotten, disconnect all the controller
power sources and any wire from
Ai1
and
Ai2. Short then
Ai1 to
Ai2 with a piece of wire and
power-up the controller again and wait until the middle LED flashes
at a 1 sec ON and 1 second OFF rate.
Default settings are then
restored as in F? here just below, and the Password will be
0000 again.
See the new status information by sending [
Pw
s] and
[Pw
ss] and
check
all the settings again also restored to the default value! Ai1 is at box te
rminal (20) and
Ai2 (21).
Do not forget to disconnect Ai1 from Ai2 after that or
the password will be reset to 0000 again after any initialization.
F
Factory parameters restore.
The controller can be restored to its default factory settings. In case of a major
problem, sending command [Pw FSRA] could
solve the issue if the controller is still able to receive a command.
Wait until the middle LED flashes at
a 1 sec ON and 1 second OFF rate (if a SIM is installed) after
a Force Settings Restore All command and use then 0000 (4 x zero) as password that is also
restored. Then start to re-program
the parameters to the wanted values. Restoring the controller and the
Parameters to the default factory settings can also be achieved with
the password-lost-solution explained just above at P?.
[Pw
Fz] only initializes the GXL88 and
restarts the built-in radio and internet module, password and
parameters remain the same. This action has the same effect (but from a
distance) as removing and re-establishing the controller power.
[Pw Fg]
Initialize the radio module that connects to the GSM
network. Only use it after changing
some AT settings.
[Pw F?] shows relevant parameters.
FSRA
(x) Delete/Reset All(Not N list)!
Pw
Fz (z) restart system. (z) How many Fz so far
Use
0000 s after 30s. (x) How many
FSRA so far
See
Pw G?/G+
GXL88
V2-15
Loaded firmware version 2 2015
Amsterdam
Controller name / location
When needed, command [Code Fe] ((e)mergency) to the controler
immediately stop any radio trafic (shut off the GSM module), see also G
below. Commande [0000
sim 0 fe] will stop definitely because SIM 0 make the GXL88
works whitout any GSM trafic...
G
GSM network parameters
The most right red LED at box position (54) shows that the SIM is
registered to the GSM network when it is flashing with a brief flash at
two second rate. If not
lighting at all or each second briefly, the system can not receive nor
send SMS message or call. Use then the internet if connected to
or the serial link to PC if not. Always hold the SIM cart by the
plastic edges and not the contacts.
The reason could
be one of these:
SIM is not in the right socket, the system takes S1
by default also on two-SIM controllers (see command SIM 1 below)
SIM does not make good contact in the socket! If
clean, try to slide the SIM a half mm up and down in the closed socket
SIM is dirty. Do not put fingers on the SIM or
sockect contacts. SIM and holder can be gently cleaned with 90°
alcohol
Use a normal cell phone
to remove SIM code and test the SIM. The most simple SIM with no 3/4G
will work
Command [Code G?] will show
the following parameters:
Pw
SIM 1
SIM
mode 1(defaut) selected with [Pw SIM 1]
Mode=1 Used=1 Selected
mode and the one actually used
0,1,2,3(1+2)
Possible
modes. 0, 1, 2 ou 3(two together)
Fg
restart
GSM
radio!
[0000 fg] reset and reconnect to
network
Fe Emergency Stop! [0000 fe] Stop radio
immediately!
Ant:
36% Rx
Antenna signal. < 12% become very low!
OP:
KPN MOBILE Name
of actual connected cellular operator
IMEI: 563031015145201 International
Mobile Equipment Identity
V0:
4364 Voltage
on GSM radio module (millivolt)
T0:
33
Internal
contrôleur temperature, °Celcius
When the list is incomplete use command [0000
G+] that will first make reload the parameters before sending
the above message.
Mode SIM
0 will make the GXL88 controller to work without GSM connectivity. So SIM cards (also inserted) are ignored and all related
GSM issues are discarded. This option will be useful when the controller
is used to regulate some local systems that do not require external
control or commands. When wanted, internet or PC serial connectivity
is still available in mode SIM 0.
Regarding
the possibilities, this controller is also a programmable control
computer at very fair and competitive price!
Please note carefully that sending the command [Pw
SIM 0] to the controller via SMS enables the SIM mode 0 and will
consequently be the last SMS command received via SMS. So if the
internet mode (if available) is not enabled before by [0000
i on]
the controller will only be locally accessible via the serial link to
the PC.
[Pw
SIM x fg] where x can
be 1, 2 or 3, sent from internet PC via serial or internet will
re-enable GSM communication when possible.
Mode SIM 1 is for SIM holder at S1 and Mode Sim 2 for S2. Select preferably
SIM1 at S1 for controller having two SIM holders when only one SIM will
be used as in most cases.
So command [0000
sim 1] enables SIM 1 usage and of course its SIM voice call
number! SIM
mode 2 will be configured when SIM holder S1 is bad or dirty. SIM 1 or 2 work both the same and SIM 3 makes use the first SIM
available to connect to the GSM network.
H
H:M setting for time related functions.
To set the controller software and hardware Real Time Clock (
needed for all related Time functions) at
14:49, use [
Pw
H 14:49].
The clock can be
adjusted before or after any other command. Like here with [Pw
H 12:14 R1 Off s]
The software clock also tells about unexpected system resets. Watchdog
and control procedures will automatically reset and restart the GXL88
microcontroller on fatal software errors. By default and as control, a
Status SMS is sent to number N1 3mn after power on or initialize when
no command is received within those 3 minutes.
When the time shown in the status
is at 00:03, a system restart is notified!
After that, the software clock will synchronize with the
hardware real time clock
and automatically
be set to the right time if
parameter Hc is left at 0 and if
no power interruption has occured.
SMS [Pw h?] to GXL88 lists all time related function
settings.
Pw
H 05:38 Actual
controller time set by [Pw
H
HH:MM]
Hs1 3 12:15 Status to N3 at 12H15 once a day
Hs2
1 00:10 Status to N1 at xx:10 each hour
Hsm
0 mn Repetitive status time synchrone to Hs1 N
Hss
0 sec Repetitive status SE at sec to HS2 N1
number
He1
6 00:00
Energy SE to N6. Répetitive (00:MM) or at HH:MM
HeM
22 mn Energy status SE to N6. Répetitive on 22mn
HeS
800 sec Energy status SE to N6. Répetitive on 800sec
HL 00:00
Status to serial at
HH:MM
HrA
4 08:30 20:13 R4
ON at 8H30 off at 20:13
HrB
5 22:45
07:03
R5 ON at 22:45, stop at 07H03
Hc
0 Hg 15 Clock ±s in Mode SIM 0. GSM test time
Status message sent from the function H will show its source as
hs1, hsm, etc, at Hxx after
the controller time line (see at s?).
[Pw
Hs1 Nn 12:15] Will force a Status SMS to Nn (that can be 1 to
35), each day, at 12:15. [Pw
Hs2 30 01:30] will send a second status message to N30
at given time, so here each night after midnight at 1
hour and 30
minuts. Both cases need a valid number at position pointed numbers list
position.This
will give a good daily control of the system.
[Code HS1 2 00:15]
make the status to number N2
each hour at minutes =15. This
simply because the HH field is left equal to zero! Hs2 can do the same and both
functions can be used simultaneously
to get two status messages per hour.
So command [Code HS1 1 00:15 hs2 1 00:45] could make send
two status messages each hour
to N1.
Status SMS are sent synchronized to the minutes of the time with
Hsm function.
Hsm uses the Number programmed at Hs1.
[Pw
Hsm 11] sends a status SMS at xx:11
, xx:22, xx:33, xx:44 and xx:55 at number written at Hs1.
[Pw
Hsm 25] sends a status SMS at xx:25 and xx:50 also at number programmed at HS1.
(Hsm >2 <59mn)
Hss force sends status at Hss programmed interval value to the
number pointed by HS2 N in the
number list.
So command [Pw
Hs2 25 00:00 Hss 600]
will send the status at number found at position 25 in number list.
This on the 10 mn here, but programmable from 1 to 65000sec. Writing 0
at "25" or "600" stops the function Hss and Hs2 will be ignored because
00:00 is invalid.
An interesting option for Hss
will also be the possibility to send the status "ss" from V1. Status [s] form R1 is sent if
value sec of hss is even and status [ss] from V1 if odd. Please see [s] and [ss] again above
about the status messages.
[Password HE1 6
15:31] force reads the Power Meter and then sends an Energy Status
SMS [SE] to Number 6 in list. In this example every day at 15:31. If field HH of HsE is zero, only the minutes are worked
out and the [Se] status will be sent out once each hour at MM = Minute
of the controller enabled time clock.
So [Pw
HSE 8 00:35] makes send each hour at midnight and 35
minutes to number written in the
phone book(number list) at position 8.
(See at bottom the functions expert for the
commands [Se], [Sx ]and [Si] to the controller making it read/setting
the Power Meter.
Hem has the same synchron
functionality as Hsm above. However
the differences are that the message will be an Energie status [SE] and
that it will be sent to the
numbers indicated by HE1. See
at Hsm for He1 same timing). Parameters
Hsm and Hem can be programmed with a value >2mn and < to 59mn.
Command [Hra
2 14:15 14:30] will make switch R2 output at 14:15
On, and then switches Off
at 14:30
everyday. Function HRB
has the same functionality and here also could be used simultaneously on the same relais
output to get more switching times.
So
[Code HrA 1
00:15 08:45 HrB 1 14:00 17:15
h] could make switch same relais N1 at different times.
See also the
function "Klignoteur" that can switch very short time on big
delays.
Hc is a clock correction parameter
that can be used to
tune the
software clock only. If one thinks that the clock is too fast
with 2s every days, the command [
Pw
Hc -2] can be used. For 4s a day too slow, use command [
Pw
Hc 4].
Parameter
Hc can better be
left to 0 (zero) when the SIM mode parameter is not zero, so that
the
software clock will
automatically synchronize with the
Real
Time
Clock that does not require any
correction.
The hardware
RTC is ignored while in SIM mode 0
and only t
he software clock will then be
used, no matter the Hc
parameter value. The default
setting of Hc is 0 and SIM is 1. (see G? for
the different SIM modes).
Whatever the H parameters
settings are, the Clock(s) can always be set to the wanted time when
adding [
H HH:MM ] before or after an other
command sent to the controller. Care should be taken so that here too,
the command that makes return an answer is the last in the command
line. So for example here; [Password
N4 020452444 R1 Off H
17:51 ss].
The hardware
RTC will normally take its power from inputs: BATT V1(31), ADAPTOR VS(29) and L3/V3 at position (37) of the box. As for some customer's needs, a CR2032 3V lithium battery can be inserted in
the internal and optional receptor in order to move the controller
without losing the HH:MM time.
Hg tells at which rate
the GSM network connection control is
done. Here at 11 and synchronous to the minute. Hg can best be left to this default
value, but users can change it when wanted with [Pw
Hg MM].
Finally for menu H, any number index left at 0 or pointing to N33 will
make the function use GPRS and not SMS when transmitting the
corresponding message at programmed H timings. Please see the functions
expert file for details!
I Configuration and
internet accès. [Pw i?] for details.
Quicker and easier than with only SMS the
GXL88 can be advantageously controlled via internet. Almost all the
fonctions, parameters and settings are then
visible on one single computer screen and the system can work
simultaneously via internet and SMS via mobile phones.
For example, access from the internet will occur with
a browser or an internet navigator and an address like the following
one will be written in the address bar: http://53.123.234.50:1425/Page_Name
1425
is the assigned PORT and Page_Name
(optional) is the name of the page to be displayed. Both parameters are
chosen by the user. So
a fixed IP address is strongly recommanded because of course, the
address where to connect must be known in order to access the
controller via internet.
The default port is generally
1425 if allready set in the M53 internet module. It can
be readed when using ez-manager.
If the Page_Name is programmed,
visible with command [0000 i] to the controller, just use it after the /
The GXL88 internally generates the page to be shown on the
navigator of your choice. This because no
program nor application needs to be installed to view the controller on
any machine from anywhere. Here's a snapshot of the PC or mobile screen.
Developments were made with Firefox,
SeeMonkey and Safari, but all navigators can be used with more or less
ease (even the old Netscape!).
It is advised to ensure that
the GSM SMS traffic with the controller works before changing the
settings i via internet. If access
through the Internet became impossible because of unforeseen or simply
because a wrong configuration command is sent, an SMS command could
easily restore the internet configuration if SMS communication works.
The built-in internet module will first be configured through the
ez-manager that can view the parameters
and change the settings. The program can be found here: ez-manager. See also the web
module documentation and a copy of
the three standard configuration windows 1, 2
et 3.
Exmanager will show the
LAN (=local)
address assigned by the router. Force the router allways assign the
same local address so that you allways can acces the controller
locally. Type the the local address in your brouser:
http://192.168.178.40:1453
[Code
i]
makes list the internet settings of the controller:
iCA 88.160.241.20:1425 GXL88 IP address and PORT after the ":" *
iSA
www.nnnn.com/name Address
where GXL88 connect in client mode
iPN
Page_Name Name of the GXL88 internal internet page
iSL
no_name
GXL88 User name in client mode
iSW
no_pass
Acces Password in client mode
iPR
0
Optional, page auto-refresh
(reload xx)
iPT
0
To server connection Timeout
2x<32
3x<16 >10s >5s Parameters length from ICA to IPT
iPB
7
GXL <=> M53 communication. 7=57600 default
I ON
Tell if internet active
ON or i1 or OFF ex:[Pw i on]
Optional
parameter Internet Controller Address will be assigned with the
GXL88 internal internet module IP address when installed. This address, for example to
http://53.123.234.50:1453, is the one to write into your browser
address bar to get access to the graphic
representation of the system and therefore, also be able to control
it via the command line. This address will be readable at the router
settings.
The Internet Controller Address parameter will be
mostly used by the [Reload
sec] command. So if ICA
is not yet configured, just fill the address at the brouwser address
bar and use the [Send]
button even with an empty command line! [Send]
only uses the address bar as a destination.
As example and to set it via SMS [0000
ica 53.123.234.50:1425 i]
The i
will make you receive a control SMS back with the list i?. * ICA
parameter is only needed for the navigator screen (bottom right)
command " Reload 0 ".
iSA (optional) is the server
address where the controller needs to connect to drop its measures or
states when the internet module AND the controller are both configured
in the client mode. This mode is simply the inverse of the
normal mode where the controller server is interrogated by the browser as a client . The principle is
the same as the GPRS mode that passes through the GSM network, but
using the router and the Internet connection.
If necessary, an iSL
identification name and iSW
password can be configured to access the server. iPT will be the allowed time waiting
for the connection to the server, before dropping or cancelling the
transaction (Not used in mode
i1 or i ON).
IPN (optional) the "Page_Name"
listed at above commande i is of real importance
but still optional. It is the
name of the internet page generated and sent by the GXL88 controller to
your navigator screen.
Added to IP:Port/Page_Name all together makes the unique address where to
connect to your controller. This page name, optional, will be "Page_Name"
or "GXL88"
by default if allready programmed (to check with command [0000 i]). Do not include any space in the
name and use 15 alphanumeric characters maximum. The controller does differentiate lower
and upper cases in "Page_Name",
so it needs to be exactly spelled.
To remove the page name, send command [0000
ipn ] and note here the standard space following the
command name, but especially the second one effectively deleting the
page name. This to check within the i? message received after command [0000 i] to the controller.
With none or deleted page name address just use IP:Port like; http://53.123.244.50:1425
to access the controller or from V2-17, http://53.123.244.50:1425/-0000
ss to get a SMS like text back on your screen (see below #)
iPR may on some browsers
automatically reload the page eg [
0000
ipr 30] could refresh the page every 30 seconds. The parameter
values will be displayed in the lower right just next to "Reload" which
is 0 (zero) by default. Do not program it to too low, the minimum being
about 10 for internet and less only on
Local
Area
Network.
If by this method the connection has not been established, a blank page
will be the result! Use then your browser back button to return to the
last
displayed page again and
increase the value of the reload
parameter
IPR. However, it can best be left to 0 (zero) until we get used
to the sometimes unexpected reactions of browser, controller and
internet. Act calmly and do not click too fast and repeatedly on the
reload or send button, because the internet and especially the
controller need some time to do any command, especially when it is busy
with
the GSM traffic.
iPB is the "baud rate"
parameter and sets the
communication speeds between the
controller microcontroller and the internet IP module. IPB 47 will be
configured for a slow internet connection [
Pw
ipb 47] (9600B/s). The second [
Pw
IPB 7] (57K6) is the default setting and is the one to use for
common ADSL connections. Finally [
Pw
ipb 3] (115K2) can be used, but does not always give good
results via internet but can be used on LAN.
In all 3 cases we will locally configure the (M53 or else) Ip module
via LAN first with
ezmanager at tab
"Serial Port / Baudrate" and after that parameter iPB via SMS or
PC. Make sure in any case that the SMS mode or PC mode is working in
order to restore configurations that could unintentionally be altered.
Small difference: Try
to connect with bad IP:port will return "site not found " and with
correct IP:port but bad page name will return "connection reset".
The UTP, RJ45, network cable
or whatever we call it, will be connected to the controller RJ45
connector that accepts and automatically detects both marked as
crossover or patch, straight cable.
The LEDs of the RJ45 connector
tells about the
connection state
to the router and shows an active connection. Amongst others,
continuous green and yellow intermittent lighting means logged /
recorded to the router. If both LEDs, green and yellow, stay lighted
without intermittence, this means the connection is Active. Disconnect
the cable and reconnect for a few seconds observing the LEDs which then
also indicate the offline state and reconnect...
The web interface gives almost everything visible on a single screen at
once and
passing the mousse through a
field adds more info at the tooltips. Nevertheless,
some time will be necessary to get used
to all the shown information.
Easy
enough, the command line will accept exactly the same syntax as the SMS
or PC commands.
As seen above, pressing "Reload 0" requires
the correct definition of the
parameters iCA and optionally IPN. Button "Send" even with an
empty command line will use the browser's address bar.
If the
PMC is connected, the measurements will be
updated after having reloaded the page with the "Reload" and not by the
command "Send" unless of course the order is precisely Se, Sx or Si.
The PMC is visible on the screen if ACM > 0 and its i/o if ACi
>0. See the
functions expert.
Internet and PC mode can not
be used simultaneously on the GXL88. To resume the PC mode
command [
0000
i off] must be sent from the internet or SMS to the controller.
The [
0000
i on] sent by SMS or PC restore the internet mode. Make sure the
controller is still accessible via SMS in order to unlock an unexpected
situation especially when the manipulations are done remotely from far.
If necessary the optional
Internet module (24x20mm only) will
be plugged at its place in the controller.
Be very
careful to the insertion direction and notice the white dot on the top
left side of the module and also on the controller board. This and other manipulations
must
be done with
non-powered controller. Connecting the controller to the router
via UTP cable makes this last automatically assign a local IP address
to the controller internet module (DHCP) so that it will then be also
accessible from the LAN with
http://
Lanipadress:port/Page_Name.
The internet module assigned PORT,
here 1425 for example
via ezmanager must
also be assigned in the router t
o be
able to access the controleur from outside via internet with an address
like:
http://WEBipAddress/PORT/Page_name. See
therefore the function port forwarding in your router.
To limit the supply power and consequently the controller's internal
temperature, shown at T0 in menu
G?, do not plug in
the network module
or, if it is already installed, unplug it when the internet is not
going to be used on the controller. This module is not required when no
LAN or Internet will ever be connected. Set also the
internet parameter to
Off via command [
0000 i off]
to the GXL88.
# A new function has been added from version V2-17 in order to
solve differents cases of internet connection which will not give a
correct
graphic representation
of the controller (like on ships with internet via satelite). We will
then be able to directly use the address bar in command mode like
http://
WEBipAdresse/PORT/-Code
(cmd) So for example
http://53.123.244.50:1425/-0000
ss will make return the extanded
status directly on the screen.
So if of course the internet function is active see [
Code i on], writing
ip/port/-0000 cmd i
in the address bar will return the menu i after having executing the
command(cmd). This on the screen itself via internet independament of
sim mode. All commands are allowed and a sim is not required if the
internet connection is stable. Graphical and/or textual representations
can even be used together.
The -code (cmd) replaces the Page_name if there were any and is written
after the /. Know that if the Internet is cut (or code i off) and the
controller is in SIM 0 mode, it will only be accessible by the PC via
its serial jack. Anyway, the Internet modes or PC and GSM are all
compatible and both can work simultaneously (thus not the Internet mode
and PC serial!). One can even restart the gsm
connectivity in
mode sim 0 with the command " Fg " (see F?) Or for more safety use the
Internet mode with a sim with controller in SIM mode >0.
For Vn, Tn and Zn,
a Warning can be sent, because all can have junctions with Low/High
thresholds and also (< / >) inferior and superior edge points
configured at which they can send Alerts. Both thresholds Low / High
must of course be configured to different chosen values and generally
with the alert (< / >)
beyond the Low/High thresholds of the junction.
Alerts are messages
sent when the programmed values for
< (Low)
and > (High)
edges or thresholds are exceeded. They are simply setup with the
function name followed by the <
and > parameters. So for
the V1 example following, <11 and >14 volt, [0000
V1 11 14].
Same for Vn, Tn and Zn that all can send alerts. A received Alert SMS start with
a)
Warning messages
are optionally sent by the Junction
functions (see just below) that can switch any output from almost any
input. Warning will simply notify of a junction action when wanted, to any number on the number list N. A received Warning SMS will start
with w)
Notice that the GXL88 SMS controller is able to sent both a Warning and an Alert
message for the same event. This at same or different measured and
programmed values.
The Alarm
function, when activated with A=On, O+ or by the optionally
connected switch "button" will send an Alarm SMS message.
Alarm messages start with; !ALARM!
So, and not to be
confused at controller setup, beside status, infos and
configuration messages received on request, we can get three kind of
messages from the controller. Warnings,
Alerts and Alarms.
Important to consider for a)lert and
w)arning, when the thresholds, edges or trip values programmed at
fields {JON} and {JOFF} of a Junction in order to automatically
regulate a system (load, temperature, or other) and when a malfunction
occurs, an alert will be sent when the alert thresholds < and >
are configured beyond the threshold of the {junction}.
Please
continue with the special functions by
functionality ranking here below or
go back to the basic functions
list.
J Junctions.
Ji1 to Ji8 / L0,1,2,3 /
JV1,2,3,S / JT1,2 / JZ1,Z2 and Z3
The "Junction" functions give you the
possibility to link any input(s) or any event (Voltage, Temperature,
Level changes and others) to any one or more output(s). These
Junctions, soft but physical, add the "extended" functionality and
flexibility of the GXL88 controller.
The most simple one for example, can switch an output relais On, Off or for a time lapse, depending on
an Ain and/or a Ln input change, and others can force one or more
output actions and optionally send a warning at
programmables Vn, Tn, Zn threshold or edges values.
[Pw J?] returns an SMS
that shortly explains the principles, [Pw
JL] lists the active Junctions parameters, [Pw
Js] lists the
junction input delays for Ji1 to JL3 that uses seconds, and [Pw Jm] the unlock
parameter for JV1 to JZ3 that use minutes. [Pw JnnFx]
forces execution!
A basic Junction has 5 fields:
[{Jnn} {JON} {JOFF} {JR} {JN}]
{Jnn} The name of the
junction Ji5, JV1, JL3, JT1,
JZ2,,,
{JON} Says what to do with {JR} if {JON} goes to level
1, On or Low
{JOFF}
What to do with {JR} if {JOFF}
goes to level 0, OFF
or High
{JR}
The Relais R1 to R8 to be eventually switched ON
or OFF
{JN}
To which number (1 to 35) send the optional w)arning
We
speak of 1/0 for inputs Ai1 to Ai8, On/Off for inputs L0, L1, L2, L3
and LOW and HIGH for the inputs from V1,2,3,s, T1,2 and
Z1,2,3.
[Pw
JL]
lists active
Junction parameters (values are examples).
J On/Off R N
{JON}
{JOFF} {JR} {JN}
i1 0 0 1 3
Input Ai1, R1 Off on any change warning
to N3
i7 0 0 0
1 Only Warning
to N1 when Ai7 changes level
L2 -1 1 1 0
No R1 change when L2 On; R1 ON when L2 to Off
V1 11.0 13.0 4 5
R4 On If BATT <11,
Off If >13, Warning
to N5
VS 1 1 0 4
Grid ADAPTOR, warning to N4, no switching
R=0
T1 19.0 21.4 3
0 Temp. R3 On If <19,
Off If >21.4, no Warning
T2 3.0 38.0 3 1
Temperature Warning if below 3° and above 38°
Z1 5.0% 95.0% 4
33 Tank
Level R4 On <5%, Off >95%, Warning
to N33
Pw
JLL
Only
active listed, use JLL if more to
list!
Jn
s s R N [Pw JLL] starts the listing SMS from
J10=JL1
L2 -1 1 1 0
From Ai1 to L3 {-1}=No R change. 1 is
just ON
V1
11.0 13.0 5 0
Only R5 switches on treshold, no Warning
if 0
T1
29.0 22.0 3 0
{Inverted} keep cool with R3, No Warning!
T2
-15.0 -10.0 3 0
Relais R3 On if <-15 and Off when >-10, no w)
Z1
5.0% 95.0% 14 0 R4 OFF if <5%, ON >95%.
R=Not R if offset 10!
Z2
45.0% 66.0% 12 0 R2 OFF if <45%, ON
>66%. R12 = R2 inverted
Z3 3.3 99.9 0
0 No switching no warnings, values are
idles
Ji1-Ji8. As an example, the junction command [Pw
Ji3 1 0 4 2] to the controller will set the output relay R4 On
when the level of input Ai3 rises from Low GND to High level, it will
stop it when passing High to Low again, and in both cases it will send an SMS warning to the number programmed at
N2 in the number list. See Js
below if a delay is needed before Ai3 changes trigger the junction.
If the alarm function is active (when A On or O+) on Ai1 to Ai8 inputs and an !ALARM! message is not wanted together
with an input junction, simply reset the input delay to zero. So here
[Pw A3 0] disables the alarm for Ai3, but leaves junction Ai3 active.
[Pw
Ji3 600 0 4 0] makes set R4 On for 10 mn for Ai3 to High and stops
when Ai3 go Low again. No SMS
[Pw
Ji3 0 10 2 0] makes reset
R2 to OFF when Ai3 goes to High and sets it On for 10 sec if low. No SMS
[Pw
Ji8 -1 -1 4 10 Ji8s 0 180
N10 <NumberAtN10] will only make send a warning
to number N10 in list when input Ai8 goes to Low level for 3nm minimum.
R4 will not be switched because for the first 12 junctions from Ji1 to
JL3,
-1 specifies no output
change!
Another example to try. If we configure Ji5
and change input Ai5 to an output (with A5 to zero see R?)
with command [0000 ji5 1 0 3 0 a5 0 r5 0] any change on
R5 will be copied on R3.
From any
{Jnn} Ji1 to Ji8 and L0 to L3 fields {JON(input goes from 0 to 1)}
and {JOFF(input goes from 1
to 0)} are both capable to switch an output {JR} ON or OFF
because of a corresponding {Jnn}
input level change.
From Ji1 to JL3, field {JON} says what to do
with {JR} when {Jnn} goes from 0 to 1 and to ON for
JLn.
From Ji1 to JL3, field {JOFF} says what to do
with {JR} when {Jnn} goes from 1 to 0 and to OFF for
JLn.
We can also speak of ON / 1 and OFF / 0 for L0, L1,
L2 and L3.
So the two {JON} and {JOFF}
fields will have 1 of the 4 the commutation commands.
-Switched On if {1} or for a time lapse {On up to
65K5 sec}.
-Left unchanged when {-1} and switched Off if field say
{0}.
Command [Pw
JVS 10.0 11.0 3 17] for example will configure the JVS junction.
{R3} will be set ON by power failure and stopped when the line voltage
returns, that will give 12V again on VS via the ADAPTOR. Warning is sent in both cases to the number at
N17 in the list.
For this, the output of the delivered adaptor 240VAC to 12VDC will be
connected at VS / ADAPTOR input ( 29+ ) and ( 30- ) and plugged in the
main grid power.
Junctions Ji1 to JL3 also have
configurable input delays for both 1/ON or 0/OFF level changes.
So as an example, we want to wait 30 seconds before turning on a
generator running via R3 in the event of a grid power failure (off) and
wait 2 minutes before stop after the grid wall power is restored (On).
We will use L1 input connected with 12V positive at (35) and negative
at any GND common connection and junction JL1. Vs already having
ADAPTOR connected could do exactly same with junction JVS.
We
configure separatly or all at once the delays, junction, stop JVS and write number if a warning is wanted:
[Pw
JL1S 120 30 JL1 0 1 3 8 JVS 10.0 11.0 0 0 N8 YourMobileNumber] with, as always, 1 space character to separate all the command fields.
JS INPUT
DELAYS are programmed in seconds
[Pw
JS] shows delays for junctions Ai1
to Ai8 and JL0 to JL3.
0-1
1-0 Level change at input (0 to 1) (1 to 0)
i1 5 0
INPUT Delay de 5 sec for 0 to 1.
i2 0 180
3mn before execution of Ji2 when 1 to 0.
i3 0 0 0 0
no Input delay...
i4 240 60 Ji4, 4mn for Low
to High, 1mn High To Low
i5 0
0
i6 0
0 (0 to 1) and (1 to 0) for
Ji1 to Ji8
i7 0
0 also(Off to ON) (On to Off) for L0 to L3
i8 0
0
L0 0 0
Internal,
reserved for now
L1 120 30
120s when to ON and 30s for L1 to Off
L2 180 0
Wait 3mn
before JL2 execute when L2 OFF to ON
L3 0 100
0= no delay. 100s before execute
L3 On to OFF
Pw JnnS S
S JnnS use SECONDS 0 to 250!
For example, command [Pw JL1 -1 3600 1 10 JL1S 0 40] could set
up a junction between L1 input and R1
that will activate the relay for an hour and send a warning to N10 in the number list, when the
voltage disappears from the input L1
for at least 40s .
While (as
seen above), the fields {JON} and {JOFF} of Ji1 to Ji8 and L0 to L3
indicate what to do with outputs when Jnn simply changes level 0/1 or
ON/OFF, for JV1 to
JVS, JT1 / 2 and JZ1 to JZ3 they will indicate the threshold or
edges value at which the output will be switched.
Therefore from JV1
to JZ3 , Junction fields:
{JON} is the LOW threshold value
who will command the output {JR} ON
{JOFF} the HIGH threshold value above which {JR}
will be switched OFF
So, in a JV1 to Z3 junction, an
Output {JR} can switch ON when the input becomes LOWER than {JON} and
switch OFF when becoming HIGHER than {JOFF}, both programmed threshold
or edge parameters.
Like above, none of the fields are mandatory. Furthermore and as shown
below, the threshold values for {JON} and {JOFF} can simply be inverted as well as the
{JR} cycle. From JV1 to JZ3 and Unlock timing, that will reforce the
junction, can be setup.
[Pw JV1 11.6 14.1 3 0]
as example enables a Junction between the voltmeter V1 BATT (31) and output R3. So when the battery voltage
becomes lower than 11.6 Volt, output {R3} is switched ON and above 14.1
Volt it is switched OFF.
This junction can give a simple but effective charge control on the
outputs {Rn} , which are all equipped with a relay of 10 Ampères. No warning is
needed, so {JN} is left at zero value or else, {JN} will point to the number position of the list where to
send the warning...
(Password {JT1} {LOW_Temperature}
{HIGH_Temperature} {JR}
{JN}
This can setup a heater junction
between the (delivered) Thermometer sensors T1
and an output {JR}. This gives a simple thermostatic
control on T1(39) and/or T2(47)
no warning will be needed, but the function Tn < > can be set to gives
anomalies alert (see T?}...
Thus, here as an example the command: [Pw Jt1 18.5 20.5 3 0
T1 15.5 23.3]
[Pw JZ1 5 95 0 11]
Can make send a warning at N11 if lower than 5% and higher than 95%
level (no JR).
[Pw JZ2 10 90 2 0]
Can start a pump on R2 below 5%, fill the tank to 90% and stop (no warning JN=0).
[Pw JZ3 5 95 12 18]
Can make switch a pump to empty the tank when
above 95% and send a warning to the number at N18. R2 will stop the pump when the level comes below
5%. Note here that the field {JR} has an offset 10 so that the
commutation cycle is inverted.
[Pw
JT2 32 22 4 0]
R4 ON above 32°C and stop below 22°C. This could be used for some
cooling device which is the opposite to the T1 heater junction just
above. So {JON} and {JOFF} can also
be inverted!
[Pw JZ3 45 70 0 25]
There is no switching when {JR}=0), only a warning for above 70% because N25 is ">NUMBER".
As seen before at N? , when a
number is preceded by < or > it will only send for an Off/0/Low
or On/1/High event.
[0000 JV2 47 56 2 0
V2 46 58] configures a junction between input V2 and output R2. If the voltage V2
decreases below the setting of {JON}
(47V) at input V2 (33), R2 is then switched to ON and on the other hand
it will be swiched OFF when the voltage at the input increases above
the setting of {JOFF} ( 56V).
No warning is needed here
when just switching a charger On and Off.
If the charger does not work well (or that othetors also order
switch R2) and that the voltage drops <
46V or rises > 58V,
an Alert will be sent to N1
(and to a second number depending on parameter V1N) by the V1 < > fonction. This gives a
good control of the charger and the output...
A Junction Warning SMS message will look
like:
w) Z1/GL(43)
Shows Z1
alias, here GL for Gauge Level
HIGH = 80.1
w) for
warning. Actual measured value
Ai:
11111101 This line only when i1 to i8 junction
JUNCTION JZ1
Specifies
JUNCTION not a)lert
or !Alarm!
10.0 80.0 2 0*
Actual jz1 junction settings. (*see below)
SH110 OIL Probe Name of the FUNCTION (not
the alias)
JnnS 10 20 Optional
sec. junction delay
if i1 to L3
JZ1M 1
Optional
Mn junction delay if V1 to Z3
R2(on)=OFF Output
R's previous state and now switched
for: 5s
For how long, if timing value, when I1 to L3
Use
Pw s, J?, JL Suggests
commands related to Junction
07:10
Amsterdam Controller time at warning and
name/location
Or
for junction Ji4 for
example:
w)
PORTE d'ENTREE A/i4(24) =1 Ai:
11111101 JUNCTION Ji4
0
0 0
1
Ji4S 5 5
R0(off)=OFF etc...
Or
for Junction JVS Voltage
Supply at ADAPTOR:
w)
VS/adap(29) LOW
= 6.8 JUNCTION
JVS 7.5
11.5 2 1
WAS
GXL83x AC JVSM
0 R2(off)=ON
etc...
Junction field {JR} can first make switch an output
and field {JN} vectors/points
to the position where to find the number to send the optional w)arning (see
N?). But when a command and not a
number is written there, a following local command can be
executed.
So if the above example says 24
and not 0* at {JN} and we programme N24 with [Pw N24 =R4 180 s+31], junction
JZ1 will first switch R2 OFF(bcs >80%), R4 for 180 seconds (cmd at
N24) and finally make send a status ss to number N1
after 31 seconds. So one trigger can
switch more
than one output.
JM Unlock
timing can be setup for junction JV1 to JZ3.
Unlock
timing is programmed in minutes and is accounted for both {Low} and {High} Input level event. Unlock timing can force a junction
to trigger again and again after 0 to 250 minutes if the
previous junction action did not change anything and when the Low-High
threshold values are still outside de programmed working window, which
is of course between de {Low} and {High} thresholds. When left unused
(JnnM 0), the junction normally executes once passing the programmed triggering level
values (threshold) {Low} and/or {High}.
So in case we want to switch a pump that begins to fill a tank at 5%, stops it at 95% level and receive
a warning on N18 when doing so, we
will program a junction with [Pw
JZn 5 95 3 18 JZnM
10
N18 NumberToWarn] where n
is Z1, 2 or 3 and 10
is the wanted Unlock delay written in minutes.
The
above JZnM settings will reforce the JZn Junction each following 10
minutes. Try to start the pump again and warn
N18 again ONLY if
the level is still below 5% AND that there is a real R3 switching
(because R3 was switched off for whatever reason).
On the contrary, if the tank is still above 95%, R3 will be checked
again every 10 mn and the junction will do nothing if R3 is OFF. If
not, R3 will be switched Off and a warning will be sent
again.
For even more security we
could also setup the Zn < >
function outside
the junction edges like 4% and 96%
and get an Alert
message when the level exceeds these alert limits. To
setup an Alert, use [Pw
Zn 4 96] as an example.
Remember that junctions send warnings and < > functions send Alerts,
[Pw Jm] lists the
junction Unlock delays for JV1 to JZ3.
nn Mm
Name / Minutes. Same
delay for {JON} and {JOFF}
V1
0 Unlock delay for JV1 (31)+ Batt 12V
V2 5
For JV2(33)± voltmeter to ±90V Direct current!
V3 0
For JV3(37)+ (Second batterie input? or
L3)
VS
0
For JVS. Adaptor 240/12Vdv at (29)+ and (30)-
T1 5
Unlock delay for JT1 at (39)T (signal)
Z1
10 Unlock delay for JZ1 (gauge / Thermo /
Volt etc)
Z2 0
Unlock delay for JZ2 (gauge / Thermo / Volt etc)
Z3 1
for JZ3 (gauge / Thermo etc).. See also Z?
JnnM MMM
JnnM USE MINUTES 0
to 250!
The use of the PC program or, even better, via LAN will make a
simulation + evaluation of several combinations much easier.
Added Options
for junctions switching.
Two software
junctions J21 and J22 were added to the
Junctions 1(Ji1) to 20(JZ3). Any of the 20 first
junctions can have the {JN} field offset by a value of 100, so that
they do not vector anymore to the number list, but to another junction.
Any junction having field {JN} at 121 or 122 will point to these
software junctions J21 and J22 that are not connected to an output like
the others...
These two junctions, J20 and J21 are configurable just the same way as
the 12 first ones and can have {JON} and {JOFF} at
-1 for no
change, 0 for OFF, 1 for ON and SEC for seconds Timing, both fields
telling what to do with field {JR}.
Any junction trigger can make
execute another junction by simply jumping to it when the {JN}
vector is in range of 101 to 122 and so also to an used or unused one
(command
JL will show which junctions are active)!
A repetitive action as when a junction points to itself will escape
after 5 times.
To
make it easy, please try the basic one step Junctions at first...
In this example we configure JLn where n can be 0 to 3 with a 12V ADAPTOR connected to it.
[Pw jlns 0 60]
Waits 1mn delay for
input ON to Off
[Pw jLn 0 1 2 121] R2 OFF
if Ln On, ON if Ln to Off. Next J21
[Pw j21 -1
30 4 18] Next: R4 ON 30s when Ln to Off, Warn N18
Fields {JON} and
{JOFF} to -1 always discard
any action on {JR}and thus, as here above, if Ln goes from Off to ON
{JON} will keep R4 as it was. To make it also switch when Ln goes from Off to
ON just fill in field {JON}else than -1. The junction warning
is sent by last {JN} if
not 0.
************************************************************************************************
Un champs
{JON} ou {JOFF} à -1 annule
toute action sur {JR} et que donc ici, Ln à ON laissera R4
inchangé. Pour également avoir une action sur {JR} quand Ln passe de
Off à On, remplir le champ {JON} différent de -1. L'avertissement est
envoyé par la dernière jonction si {JN} n'est pas 0.
Donc
l'exemple suivant:
[0000 Jv1
11 13 2 121 j21 600 -1 1 122 J22
0 0 3 1
jl]
Fera enclencher R2 quand la tension à
l'entrée B1/V1(31) descendra au dessous de 11 Volt, mettre R1
en
marche pour 10mn et eteindra R3 au cas ou il serait
enclenché.
R2
s'arrête
si V1 monte à plus de 13 volt R1 n'est pas changé (à cause du -1) et R3
s'éteindra au cas ou il était
enclenché.
Notez que
l'action de passer à 13 Volt débloque la limite basse de jV1 qui pourra
de fait à nouveau fonctionner.
************************************************************************************************
JnnF1 JnnF0 Force/test
the junction execution.
To control the configuration performed on the junction, it is
possible to force their execution by simulating a change. We first take
the most simple junction example and
configure
the junction
Ji4 with [
0000
Ji4 0 0 0 1] so to get a warning to N1 for any input change 0 or
1 of Ai4. Now we can force execution by simulating 0 level on Ai4 with
command [
0000
Ji4F0] or level 1 with
[0000
Ji4F1].
For
Ji1 to
Ji8 the simulation works both
directions 0 or 1 independently of the input level or its
corresponding Js delay. For the other,
the junction condition needs to be true and the junction should have
already worked.
So for [
Pw
Ji2
0 1 2 1], command [
Pw
Ji2F0] simulates a low level
0/GND at
Ai2 input and
so forces
junction Ji2 to switch R2 On. When not, it is already On of
course. On the contrary, command [
Pw
Ji2F1] will
force
junction Ji2 to stop relay R2, because fields {JON } = 0 which
means Off or 0.
So here again clearly,
1 at the input activates the
field {
JON} and
0 activates the field {
JOFF} of the junction function.
For JV1 to JZ3, JnnF1 activates field
{JON} and JnnF0 activates field {JOFF}. To simulate the
junction
VS, the voltmeter at
box input (29)+ (30)-, send J
VSF1
or
JVSF0. If, of course, the
junction has already been configured as for example like
[
JVS
9.9 11.1 0 1].
K Interval timing on Rn. [Pw
I?] gives the details.
One of the four relay Rn outputs can be used as a flashing, Klignoteur in Flemish and Dutch (the GXLxx
were designed in The Netherlands). One of the 4 Ai5 to AI8 inputs can also be used when the input is
configured as an output. See therefore at menu R.
[Pw
K3 40 3600] turns on the R3 output for 40 seconds , stops ,
waits 3600 (1H) and restarts again for 40s and so on, until the [Pw
K0 0 0] command which resets the function to idles state or
another R or timing value like [Pw
K4 40 3600].
Note that when
the klignoteur
is running, a status will show the remaining time ON and remaining time
Off next to the corresponding output. The cycle starts with putting the
relay to On. Do not choose too short flashing time in order to spare the mechanical
relay output!
The maximum delay of kr On or Off can be up to 65k6s
maximum, where 65500 seconds will make a time laps > to 18H. If the function k
is used on one of the 4 inputs AI5
to Ai8 configured as an output, the On/Off time can be reduced to a minimum of 1 second.
Take the case of input Ai5 transformed into R5 output as seen in R?.
So the entry delay is set to 0 by sending the [Pw
A5 0 K5 4 8]. This
would make the output R5 4 seconds On (level 1) and 8 seconds OFF
(level 0).
As a test, a 10 mm "low power" LED (we can provide the LED for free) can be connected
directly to AI5 and GND connections on the right. Then send the command
[Pw
A5 0 K5 1 1] to
have one sec On and one sec Off. If the LED does not flash, just
exchange the two connections on Ai5 and GND.
M Monitor
audio [Pw M?] explains the
function.
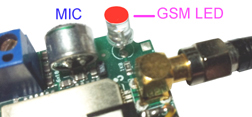
The internal microphone at position (52)
of the controller box (do not push
anything in there!) can
automatically be activated
during an alarm so that the controller can make a voice (any fixed or
mobile) phone call by itself to the outside. The MIC function can also
be setup for auto answer, so that the controller replies on normal
phone call. Review also
N at ** for more infos.
For example, first send the [Pw
M2 s] to make the controller auto answer a call (the s, optional, will return a status
message and should be visible as M2 in the
status). After that, dial the controller's SIM card number like a
normal phone and you will be able to hear around after 2 rings.
Values of M are valid from 1
to 5, but rather choose 2 or 3. Hang up to end the call, recall or
clear the function by [Pw
M0] [Pw
M9]. The MIC will deactivate itself at HH:59 +1 (so each new
hours). [Pw
s] or [Pw
m] will show the actual configuration.
M set to 9, [Pw M9], makes the
controller send back a Status short message when called. This message
is sent to the first number in the list (position N1) after two rings.
To get the status message, when M9, just normally (voice) call
the controller SIM number. The call can be terminated when the third
ring is heard.
A call request to the controller is also possible by command ! and so if we send [0000
!NumberToBeCalled], the controller will then dial the
"NumberToBeCalled" and so make a phone call to any phone with open mic.
Just hang up to complete or the controller will do so itself after a
certain time. [0000
!N8] could do the same with the number at position N8 in the
list. (see at !)
T Temperature Alert and setup for
T1 and T2. list
The thermometer function can automatically send an alert when the temperature falls below or above the
programmed edges < and >. These edges, thresholds or
limits, as we prefere to call them, are programmed by the command [Pw
T1 2.2 37.5] for example. The alert will be sent by default to
N1 (changeable), but a second
alert number could be programmed by [Pw
T1N 13] for example, which makes send the alert to the number
written at position N13
in the list of numbers.
As seen at J, we use
function JT1 when an Output
needs to be switched if the temperature exceeds programmed thresholds.